Checklist of how to Calculate Pneumatic Cylinder Force
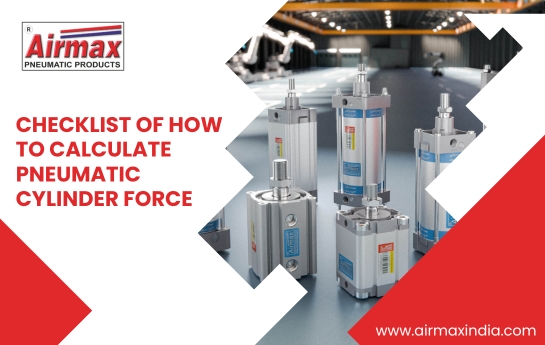
Calculating the required force of the pneumatic cylinders for your application is an important factor. Pneumatics are widely used in industries to automate processes, raise hundreds, and create motion, but miscalculating the forces required can cause performance issues, reduced efficiency, or possibly equipment damage.
Airmax Pneumatics Ltd. has prepared a detailed checklist to help you calculate the pressure in a pneumatic cylinder and match the cylinder to your specific load needs.
Understanding the power of a pneumatic cylinder
Before we dive into the calculations, let’s be aware of the basic factors that affect the power of an Pneumatic cylinder. Pneumatic cylinders convert compressed air into mechanical pressure.
This force is typically used to push, pull, or transfer mass in a variety of applications, from production lines to heavy equipment. Cylinder strength is usually affected by: air tension and bore size (cylinder diameter).
A well-known formula for calculating the output pressure of a pneumatic cylinder is:
[textForce(F) = textPressure(P) times textArea(A)]
Where:
– Force (F) is the output force in kilograms (lb) or newtons (N).
– Pressure (P) is the working stress in kilograms in accordance with the square inch (psi) or bar.
– Area (A) is the effective area of the piston (usually in square inches or square centimetres).
A step-by-step checklist for calculating the force of a pneumatic cylinder:
Let’s walk through the steps to correctly calculate the pressure of a pneumatic cylinder. This checklist will guide you through the key elements to remember and ensure you get the right fit in your application.
Determine the application requirements
1.] Determine load requirements:
Start by mastering the load the cylinder wants to move. Is it a heavy load that requires excessive force, or a smaller, lighter load that requires precision? Knowing this could give an estimate of the pressure needed.
2.] Define the type of movement:
Consider whether the cylinder needs to perform a push, pull, or lift motion. Each movement may require specific calculations for overall performance. For example, a thrusting motion against a hard and fast object may require more pressure compared to an unfixed moving load.
3.] Consider cycle speed and stroke length:
How fast do you need the cylinder to complete the cycle? Fast cycles would possibly require additional air stress to maintain speed, affecting the pressure calculation. Additionally, outline the stroke time required for your application, as extended stroke can additionally affect cylinder performance and air intake.
Output Force (Force in N : 1N = 0.1 kgf) | |||||||||||
Bore die in mm
|
Rod die in mm
|
Action
|
Working Pressure in Bar | ||||||||
2 | 3 | 4 | 5 | 6 | 7 | 8 | 9 | 10 | |||
32
|
12
|
Extend | 145 | 217 | 289 | 362 | 434 | 507 | 579 | 651 | 724 |
Retract | 124 | 187 | 249 | 311 | 373 | 435 | 498 | 559 | 621 | ||
40
|
16
|
Extend | 226 | 339 | 452 | 565 | 678 | 792 | 905 | 1018 | 1130 |
Retract | 190 | 285 | 380 | 475 | 570 | 665 | 760 | 855 | 950 | ||
50
|
20
|
Extend | 353 | 530 | 706 | 884 | 1060 | 1237 | 1414 | 1590 | 1767 |
Retract | 297 | 445 | 594 | 742 | 891 | 1039 | 1187 | 1336 | 1484 | ||
63
|
20
|
Extend | 561 | 842 | 1122 | 1403 | 1683 | 1964 | 2244 | 2525 | 2805 |
Retract | 505 | 757 | 1009 | 1261 | 1514 | 1766 | 2018 | 2270 | 2523 | ||
80
|
25
|
Extend | 905 | 1357 | 1809 | 2262 | 2714 | 3167 | 3619 | 4072 | 4524 |
Retract | 816 | 1225 | 1633 | 2041 | 2449 | 2857 | 3266 | 3674 | 4082 | ||
100
|
25
|
Extend | 1414 | 2120 | 2828 | 3534 | 4241 | 4948 | 5655 | 6362 | 7069 |
Retract | 1325 | 1988 | 2650 | 3313 | 3976 | 4640 | 5300 | 5965 | 6625 | ||
125
|
32
|
Extend | 2209 | 3313 | 4417 | 5522 | 6626 | 7731 | 8835 | 9940 | 11044 |
Retract | 2064 | 3096 | 4128 | 5160 | 6192 | 7224 | 8256 | 9288 | 10320 | ||
160
|
40
|
Extend | 3619 | 5428 | 7238 | 9047 | 10857 | 12666 | 14476 | 16286 | 18095 |
Retract | 3392 | 5089 | 6785 | 8482 | 10178 | 11875 | 13571 | 15268 | 16964 | ||
200
|
40
|
Extend | 5654 | 8482 | 11309 | 14137 | 16964 | 19792 | 26619 | 25446 | 28274 |
Retract | 5428 | 8143 | 10857 | 13571 | 16266 | 19000 | 21714 | 24429 | 27143 | ||
250
|
50
|
Extend | 9817 | 14726 | 19635 | 24544 | 29452 | 34361 | 39270 | 44179 | 49087 |
Retract | 9425 | 14137 | 18850 | 23562 | 28274 | 32987 | 37699 | 42412 | 47124 |
Measure the cylinder bore size:
The bore length is the inside diameter of the cylinder, which directly affects the output pressure. The larger the size of the hole, the larger the area that the air pressure can exert pressure on. Most manufacturers, consisting of Airmax Pneumatics Ltd, offer different hole sizes to fit different packages.
To calculate piston location (A) based on bore size:
- Find the bore diameter.
- Calculate the area using the system:
[textArea ( A ) = pi times left( fractextBore Diameter 2 Right )^2]
For example, a cylinder with a bore diameter of two inches may have an area of approximately 3.14 square inches.
Define Operating Air Pressure:
Operating pressure is any other key issue in determining cylinder pressure. Most pneumatic systems operate between 60 and one hundred twenty psi. Airmax Pneumatics Ltd. recommends checking the maximum and minimum stress limits of your gadget to ensure that the cylinder will operate in your preferred pressure range.
For example, if your machine runs at 80 psi, that degree of tension will directly affect the output force. You can regulate the air stress to oscillate or decrease the pressure, but make sure you don’t exceed the cylinder’s maximum load rating.
Calculate the theoretical power output:
Now that you have both region and voltage values, you can calculate the theoretical pressure:
1.] Plug in values to components:
[textForce(F) = textPressure(P) times textArea(A)]
For example, if you have a hole length of 3.14 square inches and an air pressure of 80 psi:
[textForce ( F ) = 80 , text psi times 3.14 , textsq . In = 251.2, text lbs]
2.] Adjust for efficiency losses: In addition, actual conditions may cause a drop in friction or deformation, so it is reasonable to allow a safety margin of about 10-15%. In this way, the actual strength is sufficient to reliably deal with the weight.
Calculate the rod side of the cylinder:
If your application requires the cylinder to retract (retract), you must consider the rod view, which reduces the strong surroundings and thus the pressure. The cylinder connecting rod area has less area than the bore because the piston rod occupies a certain area.
To calculate the force on the bar surface:
- Find the location of the rod itself:
[textRod Area = pi times left(fractextRod Diameter 2 Right)^2]
- Subtract the area of the rod from the area of the hole to get the massive area on the aspect of the rod.
- Use this modified area in the force calculation formula for the correct effects.
Select a cylinder based on application conditions:
Once you have calculated the specified pressure, select a cylinder that meets these specifications. Airmax Pneumatics Ltd. offers a wide range of cylinders that are optimized for specific force requirements, bore sizes and stress scores. Ensuring that your desired cylinder matches the calculated force will result in higher overall performance, reliability and efficiency.
Important considerations when calculating the power of a pneumatic cylinder:
1.] Friction Loss Factor: Cylinders lose a small amount of power due to internal friction. In extreme precision applications, consider a slight increase in air pressure to compensate.
2.] Side Load Check: Side loads can cause more drag, reducing effective force. Avoid side loading the cylinder to maintain ideal power output.
3.] Consider Air Quality: High moisture or dirt content in compressed air can affect overall cylinder performance. Airmax Pneumatics Ltd. recommends using easy dry air for best results.
4.] Effects of temperature: Extreme temperatures can affect the stress on the air and substance in the bottle. Use pressure cylinders designed for your environment to avoid problems related to temperature fluctuations.
Understanding pneumatic cylinder force? Don’t miss our detailed guide on calculating stroke length of a pneumatic cylinder. It’s the perfect complement to mastering force calculations.
Why choose Airmax Pneumatics Ltd.?
Airmax Pneumatics Ltd. is dedicated to presenting amazing pneumatic cylinders tailored to satisfy the numerous desires of industries. With a deep know-how of pneumatic generation and a willpower to excellence, Airmax Pneumatics Ltd. gives merchandise that assure sturdiness, precision, and performance.
Our experts are right here to help you select the right cylinder based on your calculated pressure requirements and specific utility wishes. Whether you want a compact answer for a sensitive application or a heavy-obligation cylinder for a commercial gadget, Airmax Pneumatics Ltd. has an answer you could depend upon.
Conclusion
Calculating pneumatic cylinder pressure correctly is important to ensuring your equipment operates effectively and adequately. By following this checklist, you may pick the excellent-suit cylinder to your software and maximise productivity. Remember, the important elements in figuring out force are bore size and air strain, but actual-global factors like friction, air best, and facet loading additionally play great roles.
Airmax Pneumatics Ltd. is dedicated to helping industries optimise their automation techniques with outstanding pneumatic solutions.For greater facts on deciding on the right cylinder or to explore our range of pneumatic merchandise, reach out to Airmax Pneumatics Ltd, you depended on associates in the pneumatic technology.