A Beginner’s Guide to Moisture Separators: What You Need to Know
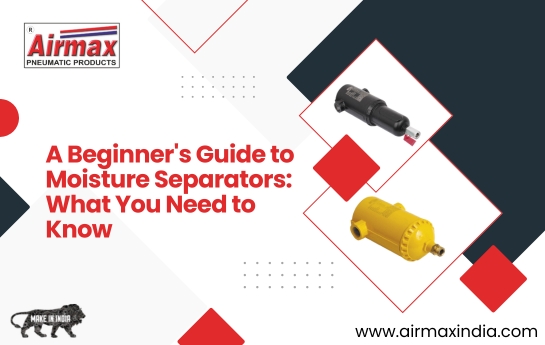
Moisture is a perpetual concern in many industrial processes, and its presence can result in severe damage and inefficiency. air compressor water separators remove moisture from gases and compressed air systems, ensuring dependable and high-performance operation. This article explores the internal functions of moisture separators, including their mechanism, advantages, and applications in industry.
How do Moisture Separators work?
Moisture separators are also known as moisture eliminators or demisters. These are the devices that are designed to separate moisture droplets from gas or gas mechanisms. These elements utilize different techniques to remove water and ensure that the downstream system receives clean, dry, air or gas.
The Role of Moisture Separators:
Moisture separator is a specifically designed component that serves as the first line of defence against condensation in compressed air systems. These pneumatic elements work by efficiently removing water droplets from the compressed air system, ensuring that only dry and clean air continues downstream. Here’s how they work:
Centrifugal Force:
Centrifugal separation involves a chamber or housing with a rotating element like a cyclone or centrifugal impeller. The centrifugal force propels moisture droplets towards the separator’s outer walls, while the dry gas or vapour continues its path. The collected water droplets drain through a separate outlet or drainage system. This process separates water droplets from compressed air, causing heavier droplets to fall to the separator’s outer walls.
Coalescing Filters:
Coalescing filters are air compressor water separators that use specialized media to merge clean water droplets into larger ones. Once larger enough, gravity helps separate them, allowing clean, dry air to pass through. These separations consist of a porous medium like a coalescing filter, which captures and merges the tiny droplets, forming larger droplets that gravitate downward, allowing them to be drained away.
Automatic Draining:
To maintain optimal efficiency, many moisture separators have automatic draining systems. These systems remove collected water at regular intervals, reducing moisture accumulation and ensuring that the separator operates efficiently.
Benefits of Moisture Separators:
Increased Equipment Lifespan:
By preventing condensation, moisture separators protect your compressed pneumatic system from the damaging effects of corrosion. This leads to a longer lifespan for your equipment, reducing the frequency of repairs and replacements.
Equipment Protection:
Moisture can cause severe damage to sensitive equipment and machinery, leading to corrosion, reduced performance, and premature failure. By effectively removing moisture separators helps to protect vital components, such as pneumatic tools, valves, turbines, and compressed air systems, from moisture-related damage.
Improved Efficiency:
Moisture-laden gas or vapour can hinder the efficiency and effectiveness of industrial processes. By eliminating moisture, moisture separators ensure that the gas or vapour stream remains dry, enabling optimal performance, improved energy efficiency, and reduced maintenance requirements.
Quality Control:
In industries where moisture-sensitive products are manufactured, such as electronics, pharmaceuticals, and food and beverage, maintaining strict quality control is essential. air compressor water separators play a crucial role in ensuring that the manufacturing environment remains moisture-free, preserving the integrity and quality of the final products.
Reduced Downtime:
Regular maintenance and the use of moisture separators help minimize unexpected downtime caused by equipment failure. This ensures a smoother and more reliable operation of your compressed systems.
Applications of Moisture Separators:
Moisture Separators find application in a wide range of industrial sectors, including:
Compressed Air Systems:
Moisture separators are commonly used in compressed air systems to remove water vapour, preventing corrosion in pneumatic tools and ensuring the longevity and reliability of air-powered equipment.
Power Generation:
Moisture separation is crucial in power plants, where steam is generated to drive turbines. Efficient moisture separation helps maintain the purity of the steam, preventing erosion and corrosion in the turbine blades and other crucial components.
Chemical Processing:
Moisture separators are designed in chemical processing plants to remove moisture from gas or vapour stream, ensuring the purity and efficiency of chemical reactions and preventing damage to sensitive catalysts.
HVAC Systems:
Moisture separators are integrated into HVAC (Heating, Ventilation, and Air Conditioning) systems to remove excess moisture from the air, improving indoor air quality and preventing mould growth.
Conclusion:
Moisture separators are essential in industrial applications by removing moisture from gas or vapour streams to optimize processes, it helps to protect equipment and high-quality output. They are crucial in compressed air, power generation, chemical processing, and HVAC systems. Aimax Pneumatics Ltd. is a leading compressors and accessories manufacturer, offering innovative performance. Investing in moisture separators ensures the health and efficiency of operations.